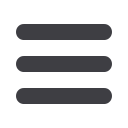
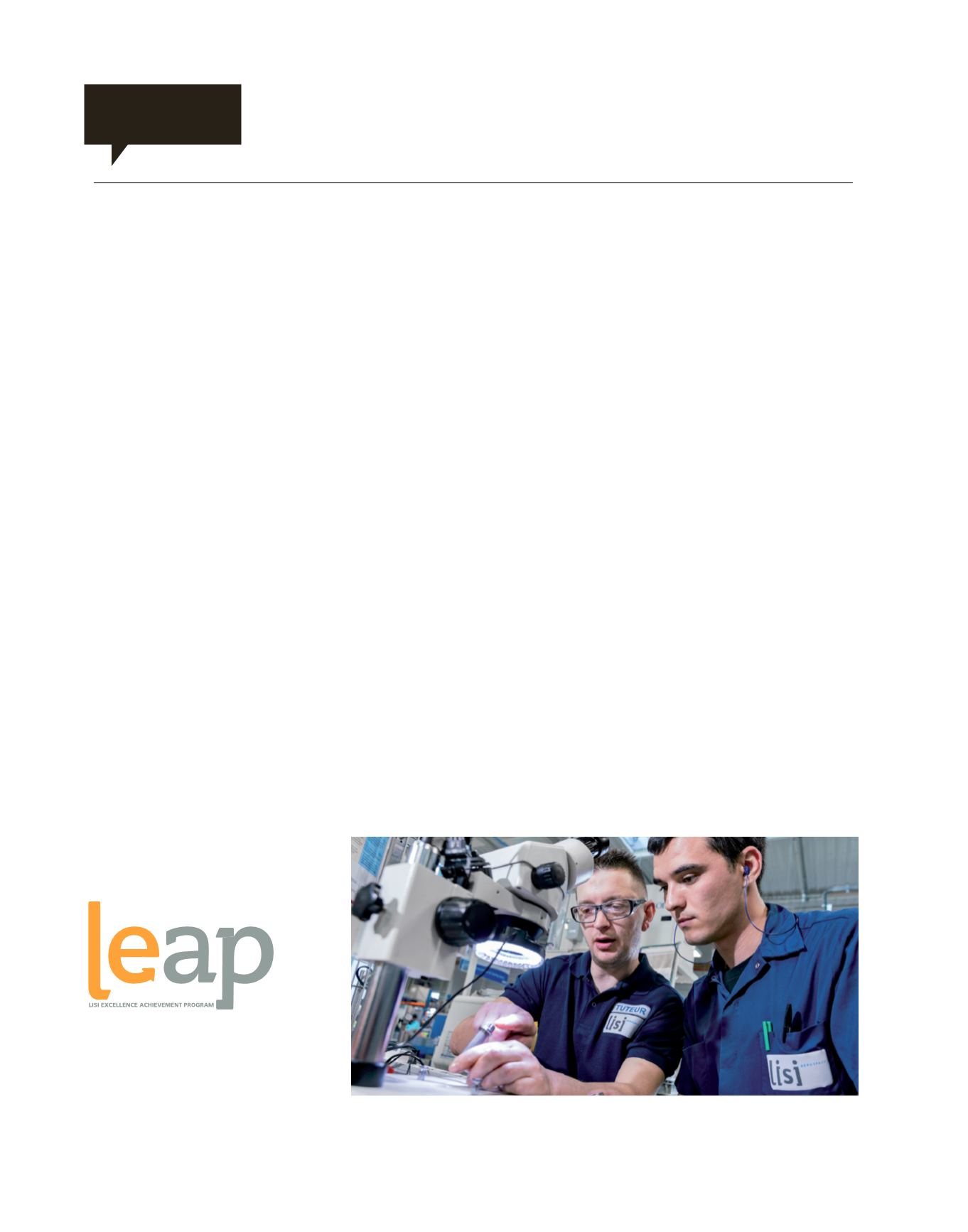
46 I
LISI 2016 ANNUAL REPORT
Performance
at the heart of the sites
_ At the heart of the LEAP, LISI Excellence Achievement
Program, performance improvement system, the PSM
method allows to support and guide the management
of the performance on the field, closer to production.
A
s early as 2011, the LISI Group
equipped itself with an
operational performance
improvement program that
is particularly ambitious.
The program, called LEAP (LISI Excellence
Achievement Program), encourages each
employee to strive for operational excellence
in all areas and in all of the company’s
business lines. At the heart of the system,
PSM – Problem Solving Methodology – is
part of the tools and methods for continuous
improvement that have been implemented in
the Group’s sites to achieve this goal. It can
handle field problems in everyday life, at the
very place where they are identified.
PSM1, closest to the field
The identification diagram of problems
and corrective decision making is based on
3 levels (see diagram page 47). Organized as
an autonomous production unit (production
line or island for example), the PSM1 is
the operational level closest to the field.
It is the cornerstone of the entire system.
It provides a response where the problem
occurs, thus preventing it from spreading to
the entire production chain. It involves and
engages all employees in solving difficulties,
in compliance with standards and set
operational objectives. But it is also the most
complex level to manage.
LEAP
ORGANIZATION
Visual management
To ensure efficiency, the organization of PSM1
was redefined in 2016. Visual management
has been improved. Simple operational
indicators dedicated to the team that is the
autonomous production group (GAP) are now
monitored, interpreted and commented daily
by the operators themselves. During the daily
Top 5 hosted by the GAP leader, everyone
can then know his or her daily performance,
discuss the problems, ponder on deviations
from the standard. The team can then look
for solutions that will address them. The
PSM1 remains to this day the most unifying
performance improvement tool from which
stems a more comprehensive approach.